热压罐操作中可能会出现温度控制、压力控制、真空系统、产品质量等方面的常见问题,以下是具体问题及相应的解决方案:
温度控制问题
温度不均匀
问题表现:热压罐内不同位置的温度存在明显差异,导致产品固化程度不一致。
解决方案:定期校准温度传感器,确保其测量准确;优化热压罐内的加热系统布局,增加循环风扇,加强热空气对流,使热量分布更均匀;进行热均匀性测试,根据测试结果调整产品在热压罐内的摆放位置。
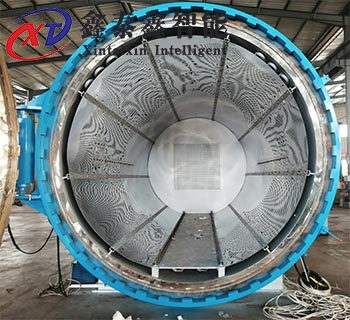
温度波动大
问题表现:温度在设定值附近大幅波动,难以稳定在工艺要求的范围内。
解决方案:检查温度控制系统的PID参数设置,进行适当调整以优化控制效果;检查加热元件是否有故障,如有损坏及时更换;确保热压罐的保温性能良好,修复发现的保温层破损处。
压力控制问题
压力上升缓慢
问题表现:在加压过程中,压力达到设定值的时间过长,影响生产效率。
解决方案:检查压力泵是否正常工作,如有故障及时维修或更换;检查管道是否存在堵塞或泄漏,清理堵塞物,修复泄漏点;确保压力控制系统的参数设置正确,适当调整加压速率参数。
压力不稳定
问题表现:压力在加压或保压过程中出现波动,影响产品质量。
解决方案:安装压力稳定装置,如稳压阀等;检查压力传感器的精度和稳定性,进行校准或更换;优化压力控制算法,提高控制的准确性和稳定性。
真空系统问题
真空度不足
问题表现:热压罐内无法达到工艺要求的真空度,导致产品内部可能存在气泡等缺陷。
解决方案:检查真空泵的性能,清理真空泵内部的杂质和油污,更换磨损的部件;检查真空管道和密封件是否存在泄漏,采用氦质谱检漏仪等工具查找并修复泄漏点;定期清洁真空过滤器,防止其堵塞影响抽气效果。
真空泄漏
问题表现:在抽真空过程中或保压阶段,真空度出现明显下降。
解决方案:对热压罐的密封面进行检查和维护,更换老化或损坏的密封圈;检查真空管道上的阀门、接头等部位,确保其密封良好;对热压罐进行整体的气密性测试,找出泄漏点并进行修复。
产品质量问题
复合材料分层
问题表现:复合材料部件在固化后出现层间分离现象。
解决方案:优化复合材料的铺层工艺,确保纤维铺层均匀、紧密,避免出现褶皱和间隙;严格控制热压罐的工艺参数,特别是温度、压力和升温速率,确保符合材料的固化要求;对原材料进行严格的质量检验,确保树脂和纤维的性能符合标准。
产品变形
问题表现:产品在热压罐处理后出现形状偏差,不符合设计要求。
解决方案:改进产品的工装设计,确保产品在热压罐内能够均匀受热和受压;优化工艺参数,根据产品的结构和材料特性,调整合适的升温、降温速率和保压时间;在产品设计阶段,考虑增加加强结构或优化结构布局,提高产品的抗变形能力。